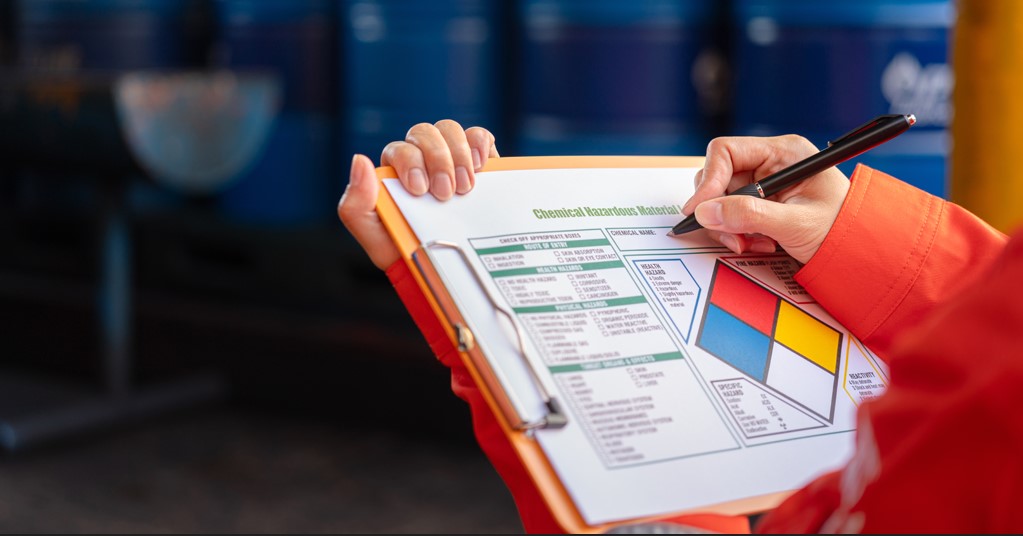
Workplace Foot Injuries: Causes, Costs and Prevention
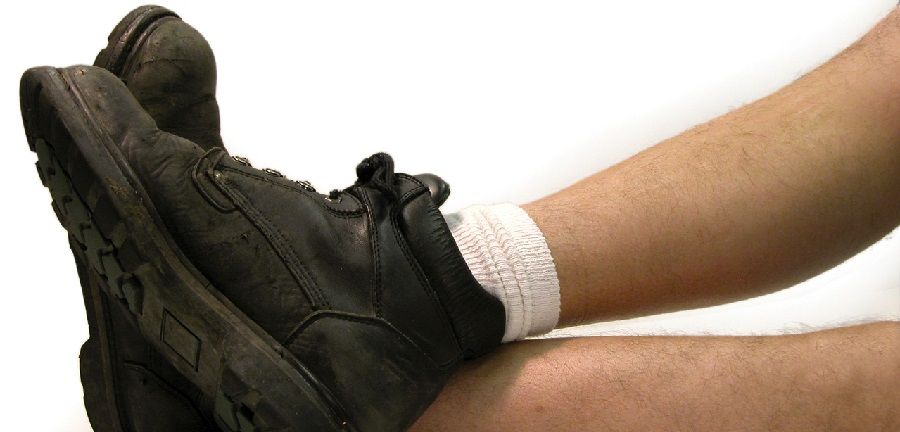
Foot injuries are among the most common workers’ compensation injuries, including breaks, fractures and heel injuries. A study of over 250,000 worker’s comp claims found the average final settlement for a foot injury is more than $17,000. The human foot and ankle contain 26 bones, 33 joints and more than a hundred muscles, tendons and ligaments, so it’s no wonder injuries to the foot can be especially painful – and slow to heal. Clearly, prevention of workplace foot injuries makes good sense for workers and employers. But safety shoes and foot PPE reminder signs aren’t enough. This article will explain the causes, costs and prevention steps you can take to reduce foot injuries in your workplace.
Causes of Workplace Foot Injuries
There are two major categories of work-related foot injuries. The first includes foot injuries from punctures, crushing, sprains and lacerations. The second includes injuries resulting from slips, trips and falls. Slips and falls do not always result in a foot injury but lack of attention to foot safety plays an important role in their occurrence.
OSHA has identified six common work-related foot injuries and causes:
- Crushed or broken feet, amputation of toes or feet – Falling objects, moving vehicles, feet trapped between objects or caught in a crack, conveyor belts
- Punctures of the sole of the foot – Loose nails, sharp metal or glass objects
- Cuts or severed feet or toes – Chain saws, rotary mowers, unguarded machinery
- Burns – Molten metal splashes, chemical splashes, contact with fire, flammable or explosive atmospheres
- Electric shocks – Static electricity, contact with sources of electricity
- Sprained or twisted ankles, fractured or broken bones during slips, trips or falls – Slippery floors, littered walkways, incorrect footwear, poor lighting
Additional foot injury hazards exist in many outdoor jobs such as logging, hydro linework and fishing.
Typical Costs of Workplace Foot Injuries
A study of workers’ comp cases in Maryland found that broken foot, stress fractures, broken toes and severe heel injuries are among the more common foot injuries. In 700 cases, the average foot injury was shown to be worth nearly $11,000 and the average permanent partial disability (PPD) award was just over $8,500. The average full and final settlement was $17,435 – but that increased more than $6,000 if it included an ankle injury. However, the actual costs vary widely case-by-case. The largest PPD award was $89,910 and the largest final settlement was $250,000.
Foot injuries often occur from falls in the workplace. Injuries from falls create a major financial strain on both employers and employees. In 2002, the National Safety Council reported that the estimated cost of workers’ compensation and medical expenses due to workplace falls was around $70 billion per year in the United States. Since this report, the cost due to fall and foot injuries has increased exorbitantly. In fact, the total cost of workplace injuries in 2020 alone was over $163 billion.
This cost includes the following factors:
- Worker productivity loss and wages
- Medical costs
- Administrative expenses
- Uninsured costs
Not only do employers have to consider the financial burden of foot injuries but they also have to consider the time lost due to workplace foot injuries. Time is lost during the day of injury, future medical treatments, and physical check-ups after the recovered worker returns back to work. In short, foot injuries have lasting effects on a workplace even after full recovery.
How to Prevent Foot Injuries in the Workplace
Employers should implement foot injury prevention policies because of the potential cost burden of workplace foot injuries. Industries with a particularly increased risk of fall injuries include:
- Healthcare: Hospitals, rehabilitation clinics, and nursing homes
- Building maintenance: Cleaning staff and janitorial personnel
- Material transport: Professional movers and junk removal services
- Construction and extraction: Building and renovation services, quarry work, mining, etc
While every employer should create precautionary policies to prevent foot injuries in the workplace, these particular industries should take even more prudent care to increase employee safety.
Foot PPE Safety Signs:
![]() | ![]() | ![]() | ![]() | ![]() |
The first step to reducing foot injuries is to identify and address relevant hazards in the workplace, and taking steps to eliminate or reduce those hazards through job and/or workplace design, including identifying proper foot and leg protection. Foot and leg protection choices include:
- Leggings to protect the lower legs and feet from heat hazards such as molten metal or welding sparks. Safety snaps allow leggings to be removed quickly.
- Metatarsal guards to protect the instep area from impact and compression. Made of aluminum, steel, fiber or plastic, these guards may be strapped to the outside of shoes.
- Toe guards that fit over regular shoes to protect toes from impact and compression hazards. They may be made of steel, aluminum or plastic.
- Combination foot and shin guards that protect the lower legs and feet, and may be used in combination with toe guards when greater protection is needed.
- Safety shoes with impact-resistant toes and heat-resistant soles to protect feet against hot work surfaces common in roofing, paving and hot metal industries.
The metal insoles of some safety shoes protect against puncture wounds.
Some safety shoes are specially designed for foundry hazards or to prevent buildup of static electricity or to protect employees from workplace electrical hazards.
OSHA Foot Safety Requirements:
- Workers must wear protective footwear when working in areas where there is a danger of falling or rolling objects or objects piercing the sole.
- Protective footwear must meet ANSI Z41 or equivalent design requirements . Note: All ANSI-approved footwear has a protective toe and offers impact and compression protection. But the type and amount of protection is not always the same. Different footwear protects in different ways. Check the product’s labeling or consult the manufacturer to make sure the footwear will protect users from the hazards they face.
- Safety shoes or boots may be required to provide special electrical conduction or insulation to prevent electric shock or static electric spark.
- Chemical-resistant boots may be required to provide protection from caustic, reactive, toxic, or corrosive materials during cleaning, or surface preparation.
- Slip-resistant soled shoes should be worn when working on slippery surfaces.
Foot Safety Tips for Workers
- Wear the correct footwear. Boots with toecaps and puncture proof soles are required in many industrial work settings. Other jobs may call for non-slip soles, chemical-resistant materials, insulation and other protective qualities. Make sure the shoes meet required safety standards.
- Practice good housekeeping. Keep the area free of clutter which can cause falls and foot injuries. Store tools and materials safely so they will not fall off work surfaces or shelves.
- Clean up spills promptly.
- Pay attention to what you are doing. Accidents causing foot injuries tend to happen when the worker is distracted or in a hurry.
- Handle chemicals with care to avoid accidental contact.
- Keep your feet, socks and safety shoes clean and dry.
As with all protective equipment, safety footwear should be inspected prior to each use. Shoes and leggings should be checked for wear and tear at reasonable intervals. This includes looking for cracks or holes, separation of materials, broken buckles or laces. The soles of shoes should be checked for pieces of metal or other embedded items that could present electrical or tripping hazards. Employees should follow the manufacturers’ recommendations for cleaning and maintenance of protective footwear.
Job and Workplace Design can also Increase Foot Safety
Effective foot injury prevention policies should include the following guidelines to increase employee safety at the workplace:
- Separating mobile equipment from pedestrian traffic and installing safety mirrors and warning signs can decrease the number of incidents that might result in cut or crushed feet or toes.
- Proper guarding of machines such as chain saws or rotary mowers can avoid cuts or severed feet or toes.
- Effective housekeeping reduces the number of incidents. Loose nails, other sharp objects, and littered walkways are hazards for foot injury.
- Using color contrast and angular lighting to improve depth vision in complicated areas such as stairs, ramps and passageways reduces the hazard of tripping and falling.
- Post safety signs in conspicuous places where safety footwear is required when there is a potential hazard from falling objects, sharp objects, etc.
foot safety Resources:
- CCOHS: Foot Comfort and Safety at Work page
- OSHA PPE guide (pdf)
- OSHA Foot Protection Standard 1910.136
- Article on foot protection and comfort in Canadian Occupational Safety
- Browse foot protection PPE safety signs and labels
- Falls in the Workplace (NIOSH/ CDC)
- Work Injury Costs – Injury Facts (nsc.org)