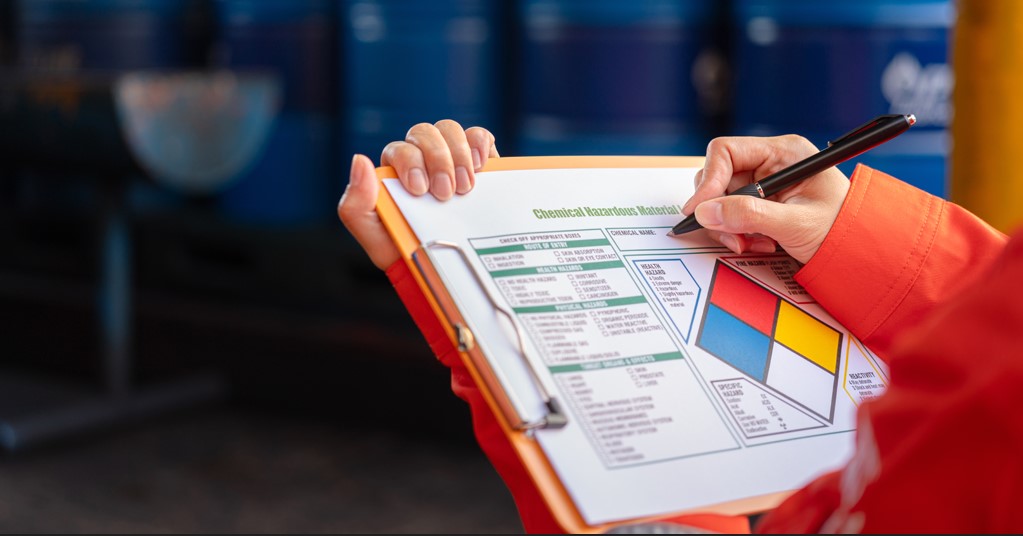
Pinch Point Tips: How to Identify Pinch Points and Protect Workers from Injury
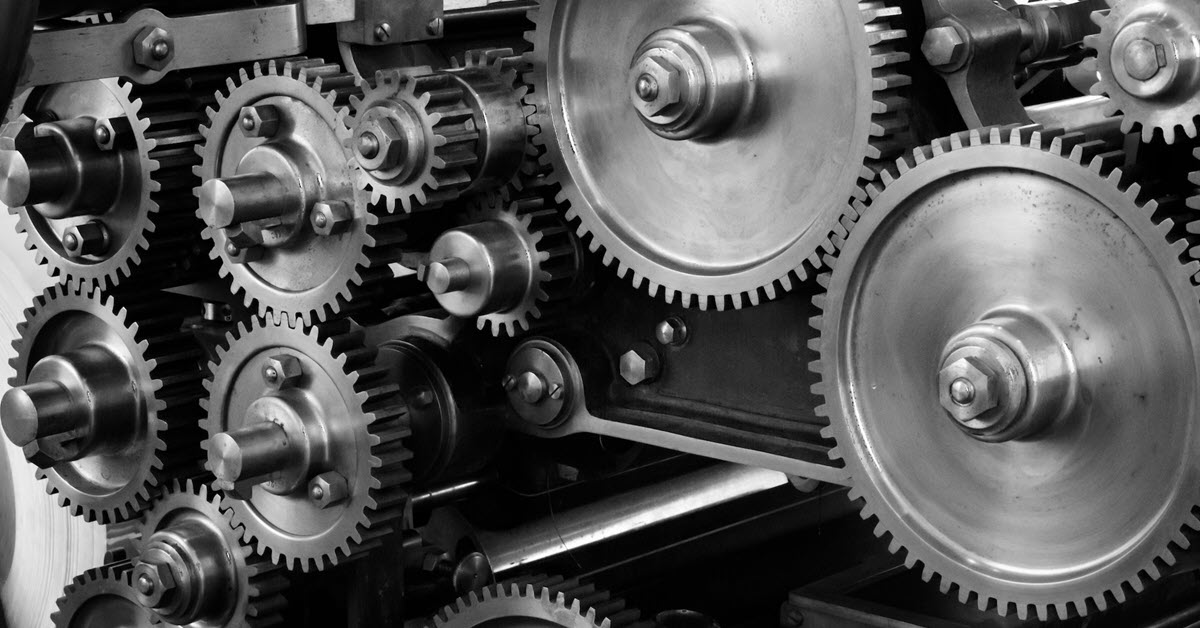
Pinch points are common hazards on factory floors and construction sites. Unfortunately, struck-by injuries involving pinch points are just as common. The good news: pinch point injuries are often avoidable. It’s important to put the proper safeguards and pinch point signage in place to keep your employees’ hands — and other extremities — safe. Read on for pinch point tips to protect workers and employers.
What are Pinch Points?
A pinch point is any point in which it’s possible for a person or part of a person’s body to be caught between two objects. Those objects can be two moving parts of a machine, a moving and stationary part of a machine, two pieces of material, material and a machine or even a tool like pliers.
Essentially, if a person or person’s body part could get trapped, crushed, cut or otherwise injured by two objects coming together, it’s a pinch point. And while pinch points tend to cause hand injuries, they can affect any part of the body and lead to more serious injuries like amputation or even death.
Three Common Pinch Point Scenarios
On the factory floor, it’s not uncommon for someone to accidentally drop something onto a machine or a conveyor belt that feeds a machine. That person might think they have enough time to reach in and scoop up the item. But a slight miscalculation could result in a crushed hand or finger.
The same goes for a warehouse worker attempting to duck under a moving overhead door before it touches the ground. Though it might appear they have enough clearance, a slip or loose shirt that gets caught on something could result in the door closing on a limb. And a lack of appropriate work gloves on a construction site might result in fingers being crushed when handling heavy concrete blocks, chains or pipes.
When speed and efficiency are tenets of your workplace, workers can be tempted to take shortcuts. But shortcuts can lead to serious injuries.
Safety training that educates workers about the dangers of pinch points will dissuade workers from taking potentially fatal shortcuts. But employers must also take appropriate precautions to provide a safe workplace by installing guards and posting signs to protect and notify employees of pinch points.
Pinch Point Safety Signs
![]() | ![]() | ![]() | ![]() |
Where Can Pinch Points be Found?
Pinch points are found all over most workplaces. Nearly all types of machinery have multiple pinch points, including rotating mechanical parts, conveyor belts, sliding components and door hinges. Pinch points are also found in overhead doors between the door and the floor and between the door and the door frame.
In warehouses and construction sites, any equipment that moves, lifts, carries or drives can cause a pinch point. Unsecured materials like chains, pipes, and concrete blocks are considered pinch points as well.
Even tools like pliers can be considered pinch points because if a worker is distracted while using them, a hand injury can occur.
Why Are Pinch Points So Dangerous?
When considering the many injuries a worker can suffer on the job, pinched fingers or a cut on the hand might not seem like a top priority. But in some cases, pinch points can cause very serious injuries. Beyond cuts, bruises, blisters and contusions, pinch points can also result in amputations, lacerations, broken or crushed bones, sprains and even death.
Regardless of the severity of the injury, pinch point injuries will likely result in missed days of work — or at a minimum, decreased productivity. That could put you behind schedule. If the injury was caused by negligence on your company’s part, it could also result in a costly OSHA fine or lawsuit. You may even see a dip in morale if workers feel their workplace is unsafe or that management isn’t prioritizing safety.
Tips to Protect Workers from Pinch Point Injuries
Workplace safety is a shared responsibility, involving everyone from the CEO down to the newest hire. There are several things that can be done at every level to ensure employees have the tools and knowledge needed to avoid injuries caused by pinch points.
1. Regularly inspect machines and guards
Too often, injuries occur because a machine is not working properly or is unreliable. Regular inspections are key to avoiding injury, so employees should be encouraged to report any issues found during inspections. When new equipment is brought in, it should be inspected for pinch points, which should be identified and addressed immediately. If you’ve already set up the appropriate pinch point machine guards, inspect them regularly to ensure they are in good working condition.
2. Eliminate the issue or install guards
Once pinch points have been identified after an initial machine inspection, first try to eliminate the pinch points if possible. For instance, if the machinery or equipment can be moved to avoid creating a pinch point with a nearby wall or another piece of machinery, you should do so. In cases where pinch points can’t be eliminated, apply pinch point warning labels and install machine guards to keep employees from reaching the pinch point.
3. Post appropriate signage
Every pinch point in your facility or at a job site needs to be identified with appropriate signs or labels. This immediately lets employees know the potential dangers that exist and acts as one of your last lines of defense against injury. Once signs and labels are hung or attached to the appropriate tools and machinery, be sure to regularly inspect, clean and replace them so the message is always clear.
4. Provide proper PPE
Many pinch point injuries can be avoided with the proper PPE, so make sure your staff has access to safety gloves, forearm guards and metatarsal guards. Loose clothing, jewelry and long hair all can get entangled in machinery and pull in the wearer, or trap them near a pinch point. You can avoid this hazard by clearly communicating your dress code so employees come to work dressed appropriately.
5. Follow lockout/tagout (LOTO) procedures
Injuries related to pinch points sometimes occur when a machine is being serviced or cleaned without following proper safety protocols. Workers must always de-energize equipment before starting any maintenance. Hang the appropriate LOTO tags so other employees know not to restart equipment. Once the machine is ready to run, be sure all pinch point guards are back in place and securely installed.
6. Hold training sessions
Make sure all employees know where the pinch points are and how to avoid them. They also need a thorough understanding of your safety protocols and pinch point safety tips. Perhaps most importantly, make sure employees know to never remove or tamper with guards and to never reach around guards to access something. Guards are only effective if they are respected. Consistent communication about pinch points and the removal of guards for maintenance is key.
7. Set up safety protocols
Pre-work inspections should include looking at safety guards to ensure they are in place and in good condition before a machine is turned on. On worksites, identify loose materials and review relevant safety practices. When materials are being moved, especially on construction sites, make sure everyone knows when and where that’s happening. You could also set up a reward system to incentivize employees to report and resolve potential hazards.
Use These Tips to Start Protecting Against Pinch Points Today
Pinch points are everywhere and it’s everyone’s responsibility to protect against them. A few simple changes will go a long way towards establishing a safe work environment, and one of the first steps is identifying and labeling pinch points. If you’re in a pinch when it comes to pinch point safety signage, ComplianceSigns can help. We have a wide variety of pinch point signs and labels for every work environment.