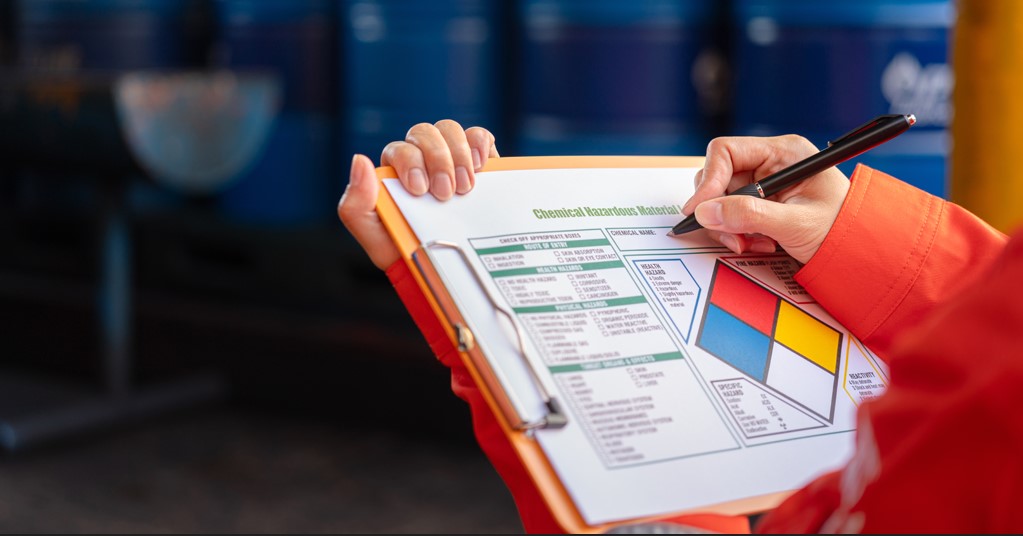
GHS Compliance: What You Need to Know
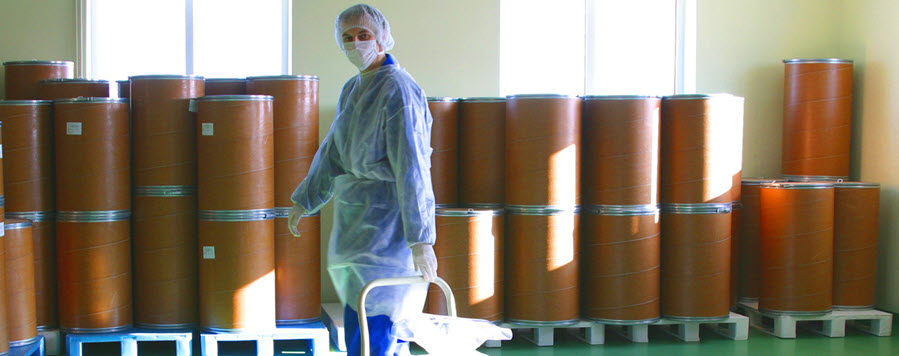
Practically every workplace has chemicals. We use them for everything from cleaning to fertilizing plants. When we use them properly they can be exceptionally useful tools to help get our jobs done. But, chemicals, by their very nature, come with some hazards.
Some chemicals react when mixed with acids. For instance, bleach mixed with vinegar or even lemon juice will start to form and release toxic chlorine gas. Some chemicals are reactive to metals or water. Other chemicals don’t need to react with anything other than the air to become dangerous.
When working with chemicals it’s vital that you know how to handle and store them. Improper handling of chemicals is not only dangerous, it can lead to a hefty OSHA fine if cited during an inspection. In 2019, a manufacturing company in Delaware had a chemical release. That chemical exposed workers to ethylene oxide, a dangerous gas. As a result, OSHA issued $262,548 in fines.
All the chemicals you use should come with Safety Data Sheets (SDS). What’s more, a Globally Harmonized System (GHS) has been created to standardize SDS around the world. Your company is responsible for meeting GHS/SDS requirements for all of your chemicals. Are you compliant?
What is SDS?
An SDS is a safety data sheet, and it’s just what it sounds like. It’s information that your supplier is required to provide to you along with any chemicals you purchase. The SDS should give you all the information you need for the safe storage, handling and disposal of your chemicals. In fact, each SDS should include the following information for GHS compliance:
1. Identification – Identifies the product, intended uses as well as information on the supplier such as name, address, and phone number.
2. Hazard(s) identification – Calls out any known dangers associated with the chemical.
3. Composition/information on ingredients – Lists the ingredients contained in the product as well as any impurities and stabilizers.
4. First-aid measures – Important first-aid information for untrained individuals including key symptoms and effects.
5. Fire-fighting measures – How to fight a fire caused by the chemical. Not all fires should be doused with water.
6. Accidental release measures – What to do if there is a spill, leak, or airborne release of the chemical. This includes the cleanup process as well as emergency measures.
7. Handling and Storage – Precautions for the safe handling of the chemical and suggestions for proper, safe storage.
8. Exposure controls/personal protection – Limits on exposure to the product as well as engineering controls or personal protection that can be used to safely handle the chemical.
9. Physical and chemical properties – This is a list of physical properties including things like color, flash point, odor and pH. There are a minimum of 18 physical characteristics that must be included.
10. Stability and reactivity – Is the chemical stable? What kind of reactions does it have to things like heat, air, water, metal or other chemicals?
11. Toxicological information – Toxicological and health effects of the chemical as well as information like likely routes of exposure.
12. Ecological information – Information on the environmental impact of the chemical. This section is voluntary, not mandatory.
13. Disposal considerations – What is the proper method for disposing of the chemical safely?
14. Transport information – Guidance for shipping or transporting the chemical by land, air or sea.
15. Regulatory information – This section is a catch-all for health, safety or environmental regulations that may not be listed elsewhere on the SDS.
16. Other information – Date of the SDS creation or update as well as information on where any changes were made from the previous version.
All of this information is critical when handling chemicals in the workplace. Not only do you need to have this information on hand, but your employees also need to understand how to find and comprehend the information on the SDS.
What is GHS?
The Globally Harmonized System of Classification and Labelling of Chemicals (GHS) began at the 1992 United Nations Earth Summit. It’s a standardized system for chemical information that can be recognized and understood across the globe. Prior to its development, every country had its own methods for labeling chemicals, which created confusion and even danger as chemicals were bought, sold and shipped internationally. GHS compliance is now required worldwide.
One of the elements of the GHS is the standardization of the SDS. The new GHS format is as listed above with the 16 categories of information. But, the GHS goes beyond just SDS. It also includes standardization requirements for product labels and hazard classifications.
To meet GHS requirements, labels for hazardous chemicals must include:
- Name, Address and Telephone Number
- Product Identifier
- Signal Word
- Hazard Statement(s)
- Precautionary Statement(s)
- Pictogram(s)
The pictograms are small pictures on the label that can help identify hazard types without the use of words, eliminating language barriers. Remember how Mr. Yuck stickers could tell a child who couldn’t read that something was dangerous? It’s kind of like that. There are nine pictograms in all, each representing a hazard classification, but only 8 are considered mandatory by OSHA. The environmental pictogram is optional but encouraged.
Your GHS Compliance Checklist
While your chemical supplier is required to supply you with current and accurate SDS, according to OSHA it is the employer’s responsibility to ensure that you have them and are compliant with GHS guidelines. Here’s a quick checklist you can use to assess your workplace situation.
- Safety Data Sheets: Make sure it’s labeled as an SDS. If it says MSDS, it’s old and not up to date in accordance with the GHS. But even if it says SDS, keep going on this list.
- OSHA HAZCOM 29 CFR 1910.1200: Classified in accordance with paragraph (d) of 29 CFR 1910.1200.
- June 15, 2016: All end users were required to comply with the GHS standards by this date. Anything older than that is not likely in compliance. Any SDS that is more than two years old, even if compliant, may be outdated. Look for updated versions.
- 16 sections: The 2012 OSHA Hazard Communication Standard requires new SDSs to be in a uniform 16 section format. The old standard was only 8 sections, so if you only see 8, you’re not in compliance.