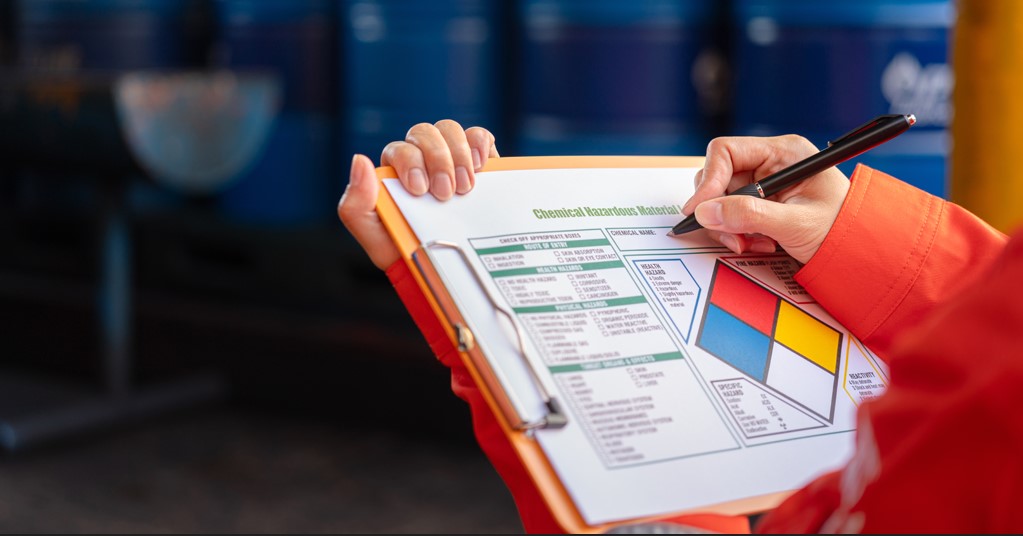
Crucial Safety Tips for Metalworking Machinery
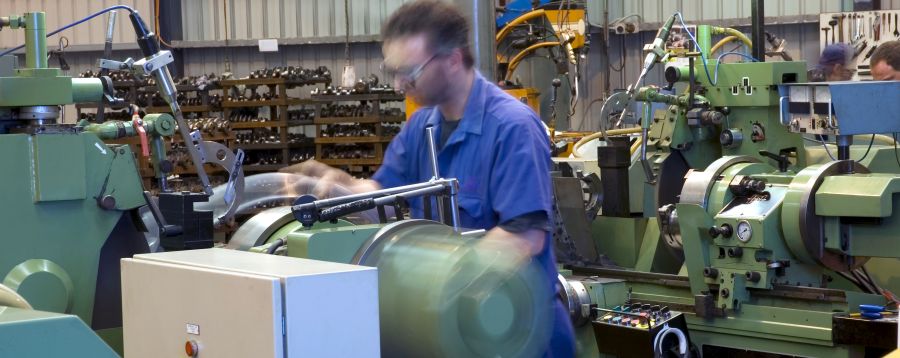
Modern metalworking machines often include a number of safety features that help make their operation less dangerous. Despite advanced safety technology, however, any kind of metalworking can still be extremely risky. Noise, vibration, pinch points, and extreme temperatures, for example, all pose serious safety risks.
The best practices will be essential in keeping workers safe. For most businesses, a few essential safety tips for metalworking machinery will help prevent accidents.
1. Use Protective Equipment and Clothing
Every day, around 2,000 U.S. workers sustain an eye injury while on the job. One in 10 of these injuries requires time off from work for recovery. Most importantly, an estimated 90% of these injuries could have been prevented with eye protection.
For metalworking, eye protection — like safety glasses and goggles — will help protect against impact by metal shrapnel and irritation of the eyes by metal dust. Welders may need specialized eyewear that provides both protection against shrapnel and radiant energy. For all workers, eyeglasses with side shields and goggles can be effective. Goggles are typically better at providing protection from impacts, dust, and radiation hazards.
Workers should avoid loose-fitting clothing or gloves, as well as accessories like necklaces, bracelets, neckties, or jewelry that can be caught in moving parts. Long hair should be tied back or confined for the same reason. Similarly, workers should avoid using rags to clean near the moving parts of a machine. Like loose-fitting clothes, these rags can easily be caught in the machine, causing injury or damage to the machine.
2. Keep Your Workspace Clean
An organized workspace tends to be a safe one – and this safety tip isn’t just for for metalworking machinery. Keeping tools and equipment organized and stored when not in use helps keep the working space clear and easy to navigate.
Cleaning up spills and removing cuttings helps reduce the risk of slipping. However, workers should wait until a machine has stopped running to clean spills or remove cuttings.
Cuttings are very sharp and should not be removed by hand due to the injuries they can cause. Vacuums, brushes, and rakes are three safer options.
Avoid using compressed air to clean dust, dirt, or cuttings from a machine or clothing. The use of compressed air can generate airborne metal particles and cause injury.
3. Use the Right Tool for the Job
Many metalworking machines are multi-use and can effectively perform a wide range of metalworking tasks. In some cases, however, you’ll want to use a specialized tool to minimize safety risks and speed up work.
To keep the cost of new equipment purchases low, investing in used equipment can help. Equipment resellers and auctions can provide you with equipment that is significantly cheaper than new machines without a serious loss in performance or equipment health.
4. Perform Regular Maintenance
Effective maintenance, cleaning, and repairs help prevent downtime and serious safety risks. Work equipment failure is not an uncommon cause of injury. When work equipment is damaged or poorly maintained, it can also behave erratically, making it harder for workers to work around it safely.
All tools and machines should be cleaned after use. Inspecting tools and machines before use can help ensure they are clean. Additionally, machines should be fully stopped and powered down before cleaning. Routine maintenance is among our top safety tips for metalworking machinery — and other machines, too.
5. Lockout Before Maintenance and Repairs
During maintenance, workers can be especially vulnerable to injury. They’re much closer to the machine’s moving parts than they would be during normal operations, and much more likely to be injured if a machine unexpectedly begins moving.
Proper lockout-tagout procedures can help reduce or eliminate the risk of an unexpected release of hazardous energy during maintenance and repair procedures.
When traditional lockout measures aren’t possible — for example, when there are no energy isolation points that can be secured with padlocks, chains, or similar hardware — alternative strategies exist. Even something as simple as having an authorized person unplug a machine and hold the plug during maintenance can help prevent a machine from powering up.
Tagout provides information to other employees on when lockout measures were applied, why they were applied, and who applied them. Effective tagout measures help ensure locks are not removed before maintenance is complete.
Staying Safe When Using Metalworking Machines
Good safety practices can help reduce some of the most serious safety risks metalworking machines can pose. Covering the safety basics — with good protective clothing, eyewear, and a clean workspace — will help significantly.
Effective maintenance should provide additional protection against injury. So long as maintenance workers follow lockout/tagout procedures, they should be at little risk of harm during maintenance and repair procedures. Follow these safety tips for metalworking machines to help keep your workplace accident-free.
About the Author:
Evelyn Long is the editor-in-chief of Renovated, a web magazine for real estate and construction professionals.