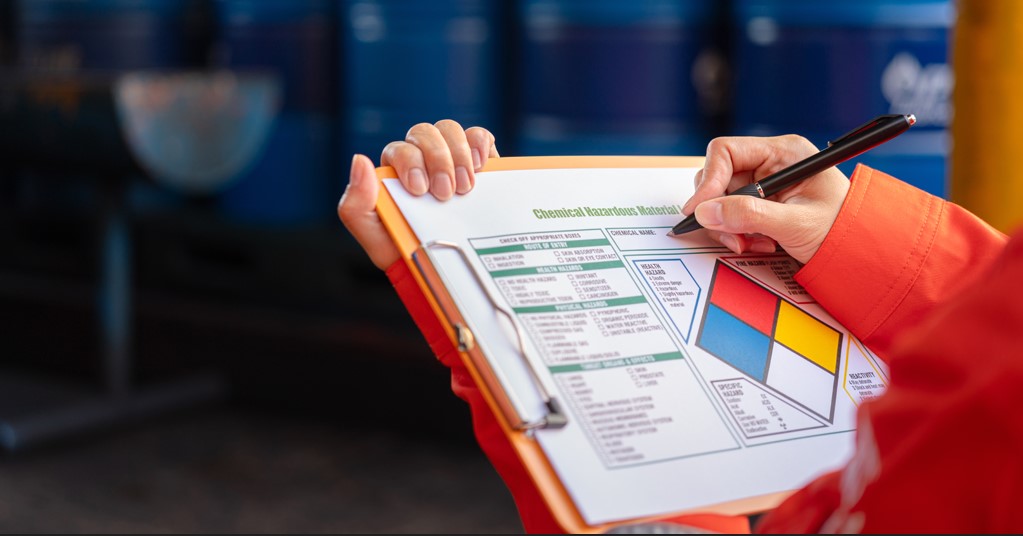
Best Practices for Forklift Safety
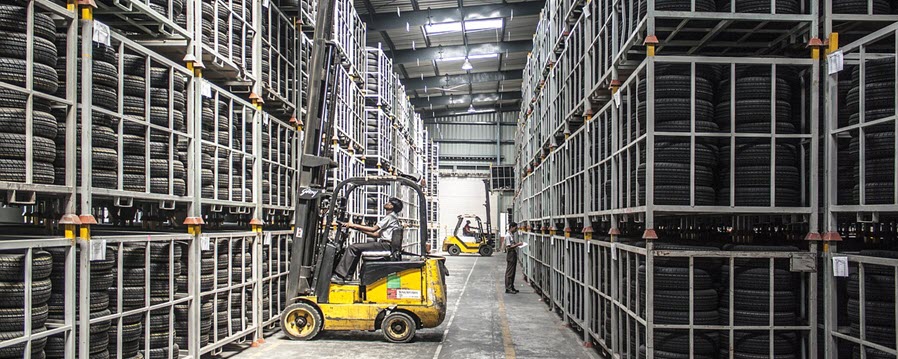
Every June brings National Forklift Safety Day, sponsored by the Industrial Truck Association, which provides an opportunity to promote safety discussions and to encourage federal legislators to consider forklift safety efforts.
The National Safety Council reports that the average direct cost to a company for a forklift incident is $38,000 with an additional $150,000 in indirect costs. OSHA statistics from 2013 show there are approximately 85 forklift fatalities and 34,900 serious injuries every year. Tipping of the vehicle accounts for more than 40 percent of forklift fatalities, and many injuries stem from failure to use a seatbelt, which is required by OSHA.
Training is critical for safe forklift operation.
It is a violation of Federal law for anyone under 18 years of age to operate a forklift or for anyone over 18 years of age who is not properly trained and certified to do so. Powered industrial trucks are addressed in specific OSHA standards for the general industry, construction, marine terminals, and longshoring. Twenty-five states, Puerto Rico and the Virgin Islands have adopted their own OSHA-approved standards and enforcement policies.
In addition to adequate operator training, forklift maintenance and operation checklists can greatly improve mechanical and operator safety:
Under the hood:
– batteries
– belt tension
– brakes
– coolant level
– fuel level
– fuel line leaks
– hoses
– motor oil
– power steering
In the driver’s seat:
– Clutch
– gauges/controls
– horn/safety devices
– mirrors
– steering
Safety walk around the unit:
– all lights
– coupling devices
– directional signals
– drive line
– forks
– fuel tank
– hydraulic lines & reservoirs
– lug bolts
– rollover protection system
– steering mechanism
– tires
– warning lights
– wheels